Hot-Gas Filtration
We ensure clean airDecades of manufacturing competence for the refractory product industry, especially in the field of high-temperature insulation wool, have resulted in sophisticated vacuum-formed shapes for high-temperature applications. The micro-porous ceramic material brings its properties to bear in the field of filtering industrial flue gases.
Your benefits
- Better energy balance / saves time and money:
No down- and up-regulation of the exhaust gas temperature necessary - Greater process flexibility:
Multifunctional use of the hot-gas filter - Space-saving and economical
- Meets highest emission protection requirements
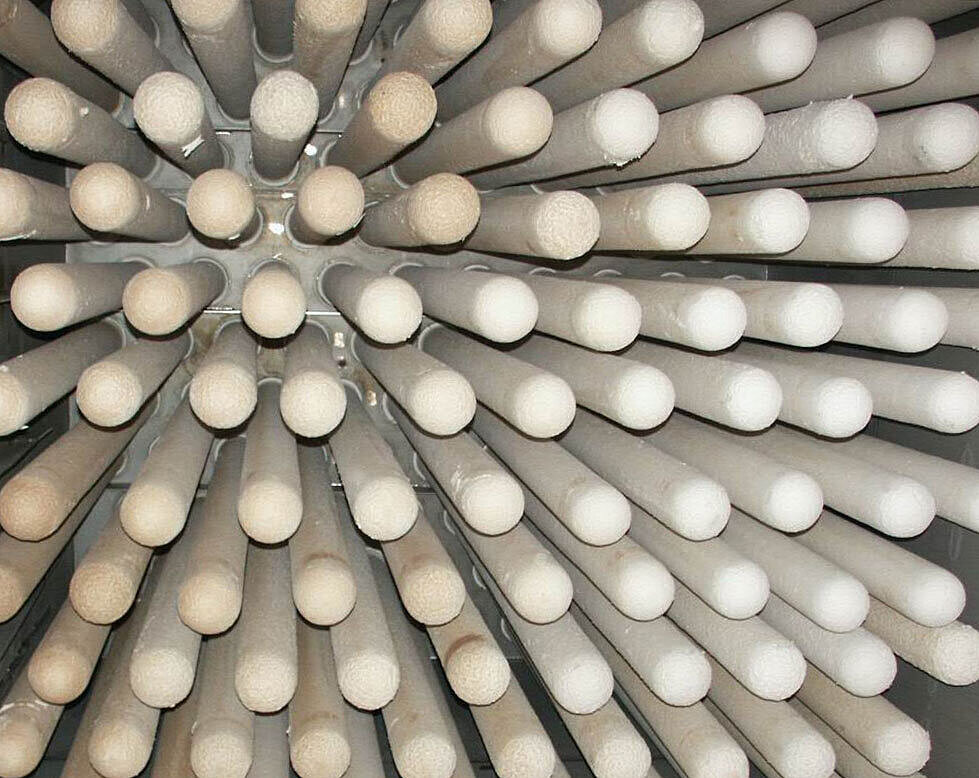
Product features
EFFICIENT AND ENVIRONMENTALLY SOUND
Removing dust from particulate-contaminated exhaust gases early at high temperatures is a requirement that makes sense not only from an economic, but also from an ecological point of view. While synthetic fabric filters reach their performance limit at around 260 °C, ceramic filter elements allow exhaust gases to be filtered up to 1000 °C. Uneconomical cooling of the exhaust gases exclusively for filtering is obviated.
By now, hot-gas filtration in industrial processes is being used for more than just air pollution control. Apart from complying with official environmental regulations, plant operators can feed back valuable raw materials (dusts) to the production process by filtering them from the exhaust air, thus increasing the efficiency of their plant and conserving raw material resources. Dust removal at high temperatures also enables use of efficient systems for heat recovery or power generation.
3-IN-1 SOLUTION: SUSPENDED MATTER GONE, NITROGEN OXIDES GONE. CLEAN AIR REMAINS.
The perfect 3-in-1 solution for complex yet simplified gas treatment is catalytically coated hot gas filter cartridges. The catalytic coating together with the variable length results in multifunctional solution combinations: “3-in-1” pollutant mixtures (DeDust, DeSOx, DeNOx) can be treated highly effectively in a single step. So the cartridges filter dust, the sorbent for desulphurization, and at the same time also reduce the levels of nitrogen oxides. For you, this means fewer interfaces, reduction in the total plant area, and thus significant CAPEX and OPEX savings.
CERAMIC FILTERS PERFORM BETTER
By using ceramic filters, you are investing in the future. Textile filters work well for some installations, but they have their limitations. For medium-sized and large plants, it is advisable to use ceramic filter elements, as these ensure consistently stable and optimum filter properties over the entire temperature range and can therefore be used in your existing exhaust gas process without any change in temperature. With ceramic filter cartridges you are also ready for the future because you can easily adjust your process temperatures up to 1000 °C without having to consider the downstream filtration stage.
• 250–1,000 °C for non-catalytic coatings (FILTRATH®)
• 250–420 °C for catalytically-coated filter elements (FILTRATH®CAT)
EASY TO INSTALL – VARIABLE LENGTH | 1–6 METERS
Existing filter systems can also be adapted to the changed conditions. The key to success lies in the filter area. You can increase this by using longer filter elements. Filter cartridges up to 6 meters in length can be inserted into your existing system with manageable expansion costs – provided the filter tank is high enough. Even if the ceiling height is not sufficient, thanks to the patented and proven Screw-and-Glue® system RATH filter cartridges can be delivered in 1-meter elements, and assembled and installed on site.