Interview with Robert Nusszer Head of Sales Glass, RATH
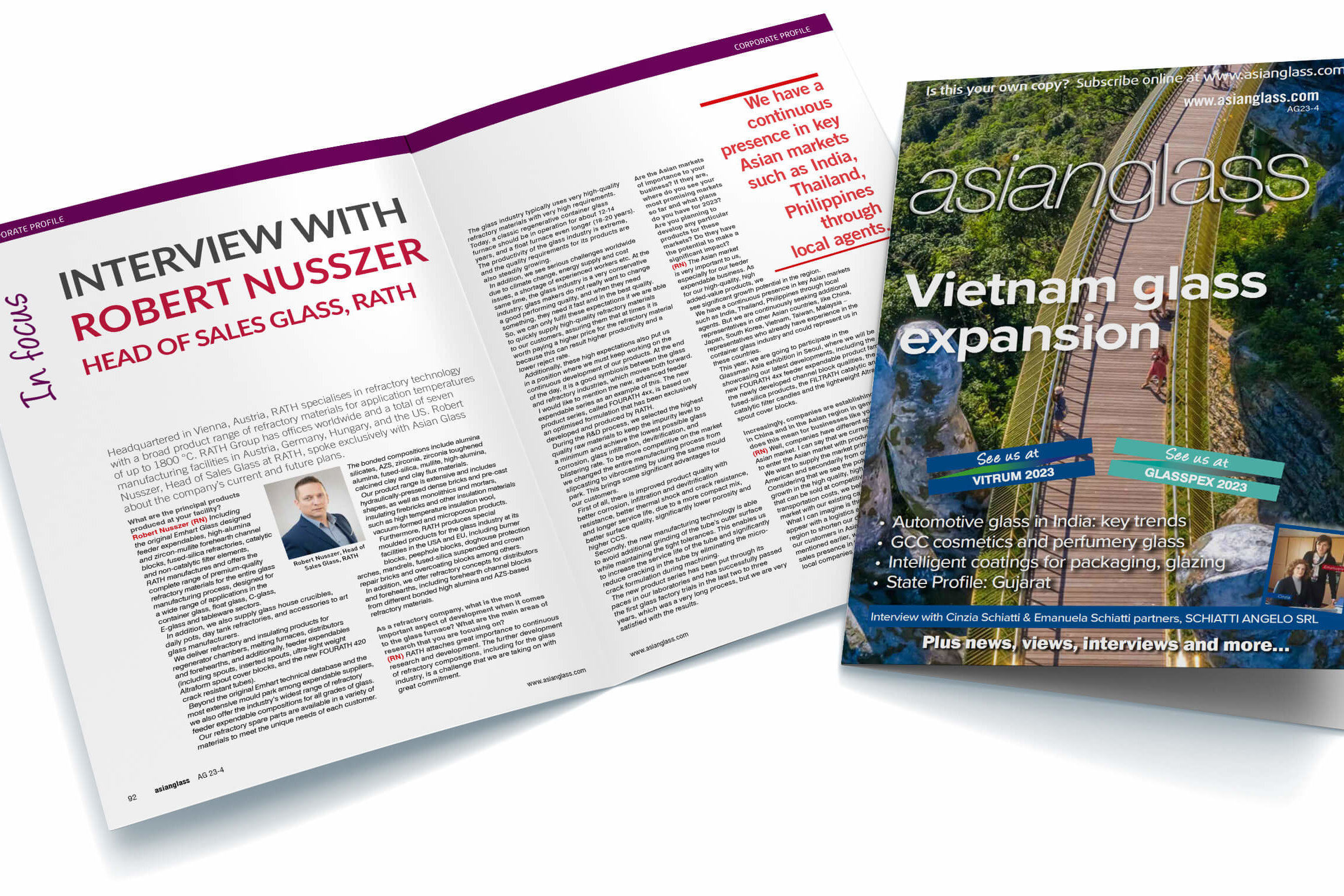
What are the principal products produced at your facility?
Robert Nusszer (RN) Including the original Emhart Glass designed feeder expendables, high-alumina and zircon-mullite forehearth channel blocks, fused-silica refractories, catalytic and non-catalytic filter elements, RATH manufactures and offers the complete range of premium-quality refractory materials for the entire glass manufacturing process, designed for a wide range of applications in the container glass, float glass, C-glass, E-glass and tableware sectors. In addition, we also supply glass house crucibles, daily pots, day tank refractories, and accessories to art glass manufacturers. We deliver refractory and insulating products for regenerator chambers, melting furnaces, distributors and forehearths, and additionally, feeder expendables (including spouts, inserted spouts, ultra-light weight Altraform spout cover blocks, and the new FOURATH 420 crack resistant tubes). Beyond the original Emhart technical database and the most extensive mould park among expendable suppliers, we also offer the industry’s widest range of refractory feeder expendable compositions for all grades of glass. Our refractory spare parts are available in a variety of materials to meet the unique needs of each customer.
The bonded compositions include alumina silicates, AZS, zirconia, zirconia toughened alumina, fused-silica, mullite, high-alumina, calcined clay and clay flux materials. Our product range is extensive and includes hydraulically-pressed dense bricks and pre-cast shapes, as well as monolithics and mortars, insulating firebricks and other insulation materials such as high temperature insulation wool, vacuum-formed and microporous products. Furthermore, RATH produces special moulded products for the glass industry at its facilities in the USA and EU, including burner blocks, peephole blocks, doghouse protection arches, mandrels, fused-silica suspended and crown repair bricks and overcoating blocks among others. In addition, we offer refractory concepts for distributors and forehearths, including forehearth channel blocks from different bonded high alumina and AZS-based refractory materials.
As a refractory company, what is the most important aspect of development when it comes to the glass furnace? What are the main areas of research that you are focusing on?
(RN) RATH attaches great importance to continuous research and development. The further development of refractory compositions, including for the glass industry, is a challenge that we are taking on with great commitment.
The glass industry typically uses very high-quality refractory materials with very high requirements. Today, a classic regenerative container glass furnace should be in operation for about 12-14 years, and a float furnace even longer (18-20 years). The productivity of the glass industry is extreme, and the quality requirements for its products are also steadily growing.
In addition, we see serious challenges worldwide due to climate change, energy supply and cost issues, a shortage of experienced workers etc. At the same time, the glass industry is a very conservative industry; glass makers do not really want to change a good performing quality, and when they need something, they need it fast and in the best quality. So, we can only fulfil these expectations if we are able to quickly supply high-quality refractory materials to our customers, assuring them that at times it is worth paying a higher price for the refractory material because this can result higher productivity and a lower reject rate. Additionally, these high expectations also put us in a position where we must keep working on the continuous development of our products. At the end of the day, it is a good symbiosis between the glass and refractory industries, which moves both forward. I would like to mention the new, advanced feeder expendable series as an example of this. The new product series, called FOURATH 4xx, is based on an optimised formulation that has been exclusively developed and produced by RATH.
During the R&D process, we selected the highest quality raw materials to keep the impurity level to a minimum and achieve the lowest possible glass corrosion, glass infiltration, devitrification, and blistering rate. To be more competitive on the market we changed the entire manufacturing process from slipcasting to vibrocasting by using the same mould park. This brings some significant advantages for our customers.
First of all, there is improved product quality with better corrosion, infiltration and devitrification resistance, better thermal shock and crack resistance, and longer service life, due to a more compact mix, better surface quality, significantly lower porosity and higher CCS.
Secondly, the new manufacturing technology is able to avoid additional grinding of the tube’s outer surface while maintaining the tight tolerances. This enables us to increase the service life of the tube and significantly reduce cracking in the tube by eliminating the microcrack formulation during machining.
The new product series has been put through its paces in our laboratories and has successfully passed the first glass factory trials in the last two to three years, which was a very long process, but we are very satisfied with the results.
Are the Asian markets of importance to your business? If they are, where do you see your most promising markets so far and what plans do you have for 2023? Are you planning to develop any particular products for these markets? Do they have the potential to make a significant impact?
(RN) The Asian market is very important to us, especially for our feeder expendable business. As for our high-quality, high added-value products, we see significant growth potential in the region. We have a continuous presence in key Asian markets such as India, Thailand, Philippines through local agents. But we are continuously seeking additional representatives in other Asian countries, like China, Japan, South Korea, Vietnam, Taiwan, Malaysia – representatives who already have experience in the container glass industry and could represent us in these countries. This year, we are going to participate in the Glassman Asia exhibition in Seoul, where we will be showcasing our latest developments, including the new FOURATH 4xx feeder expendable product family, the newly developed channel block qualities, the fused-silica products, the FILTRATH catalytic and noncatalytic filter candles and the lightweight Altraform spout cover blocks.
Increasingly, companies are establishing factories in China and in the Asian region in general. What does this mean for businesses like yours?
(RN) Well, companies have different approaches to the Asian market. I can say that we currently have no plans to enter the Asian market with production capacities. We want to supply the market primarily from our American and secondarily from our European factories.
Considering that we see the potential for higher volume growth in the high quality, high added-value products that can be sold at competitive prices despite high transportation costs, we believe that we can serve the market with our existing capacity.
What I can imagine is that sooner or later, we will appear with a logistics and warehousing base in the region to shorten our delivery times and thus serve our customers in Asia more quickly. However, as I mentioned earlier, we primarily want to strengthen our sales presence in the region through cooperation with local companies and agents.
Given that you were founded in 1891, you have a long history – how have the years been? In your opinion, what is or have been your greatest achievements to date? How do you envision your future?
(RN) Indeed, RATH, which is still a family-owned business, is more than 130 years old. I have always valued such family-owned businesses, companies that have been run by several generations of one family over decades and centuries, of which there are plenty in the glass industry as well. Their age, history, tradition and stability are worthy of respect.
A lot has happened for our company in more than 130 years. I would like to mention two points here:
firstly, the rapid development of the company in the 1990s after the liberation of the socialist countries of Central and Eastern Europe, and secondly, the acquisition of the factory in Owensville (Missouri, US).
With the latter, we were able to acquire significant know-how, a worldwide market for expendables, and gained significant production capacity. So, with the help of this acquisition, RATH has become a well-known and even more recognised company and supplier in the glass industry.
But let us also look ahead at this point: RATH manufactures a wide range of products at a total of seven production sites in Europe (Austria, Hungary, Germany) and the US. As a premium supplier in the field of refractory materials, we attach great importance to high-quality products as well as individual solutions.
An important key to the latter is our high consulting competence based on comprehensive engineering know-how. In order to be able to guarantee this high quality at all times, we also focus strongly on the continuous development of our products – as already explained with the example of the new feeder expendables series.
We also place great focus on the topic of sustainability: RATH is very committed to advancing environmental protection and helping its customers in the glass industry achieve their ambitious environmental goals. Thus, RATH continuously invests in research and development and strongly pushes the development of energy-saving refractory materials.
A constant, strong focus on quality, consulting competence, innovation and sustainability, in summary, we could say that this is our answer to the current developments on the market.
Having acquired the Bucher Emhart refractory production plant in Owensville, RATH now has a location to produce refractory and wear-parts used in the container glass industry. Do you have any current product news to share?
(RN) In addition to the development and introduction of the FOURATH 4xx feeder expendable product family, we have recently resumed the production of forehearth 333 channel blocks at our facility in Owensville (US). The channel blocks are manufactured using the original 333 formulas with the original casting technology, which made the mix popular on the market from Europe to the US and Asia.
Currently, there is a shortage of high-quality channel blocks on the market. The 333 with its fine selection of raw materials, with its very low impurity and low zircon-oxide level, but with excellent glass corrosion resistance can be a good answer for all the requirements of container glass manufacturers.
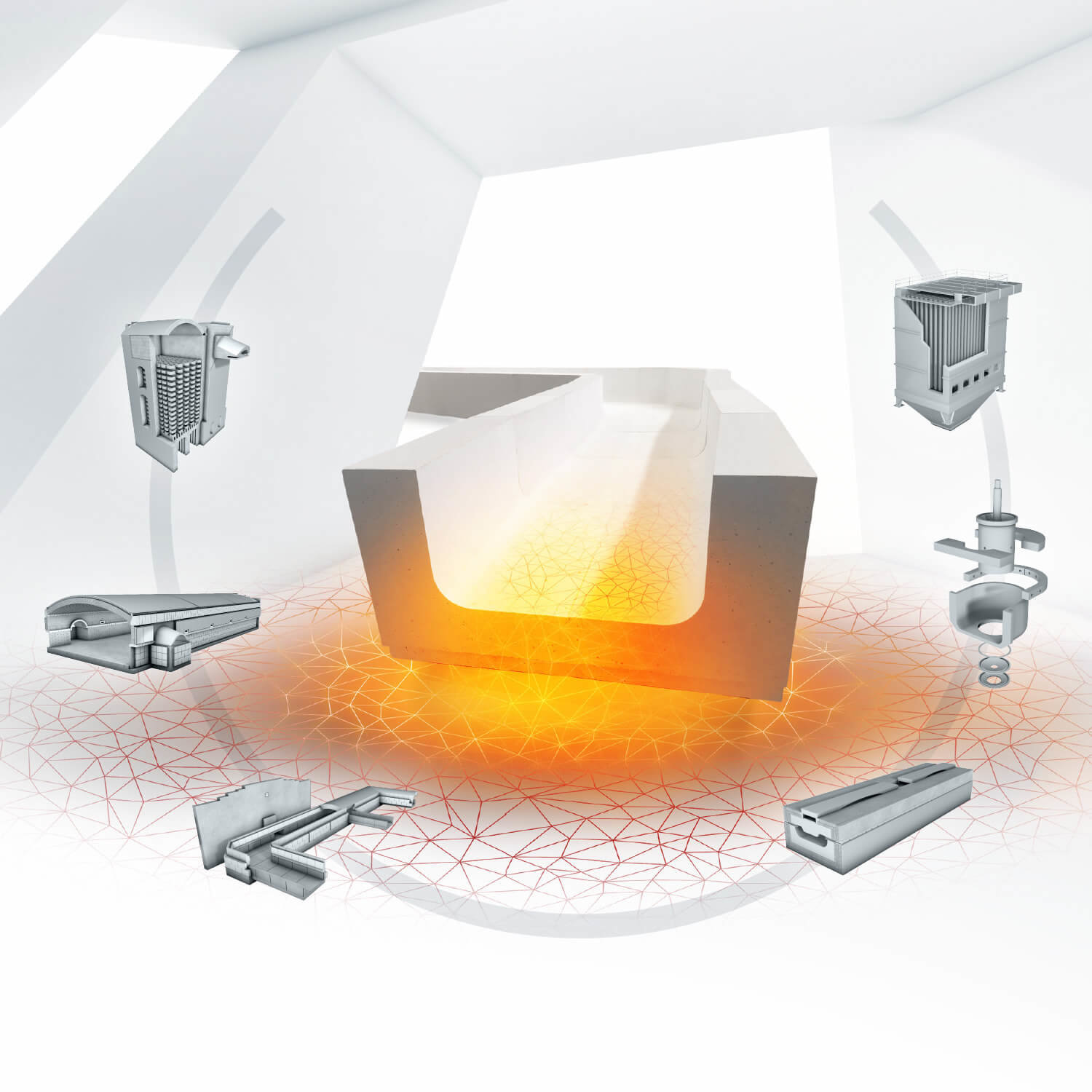