RATH reduces CO2 emissions by 70% in silicon carbide production
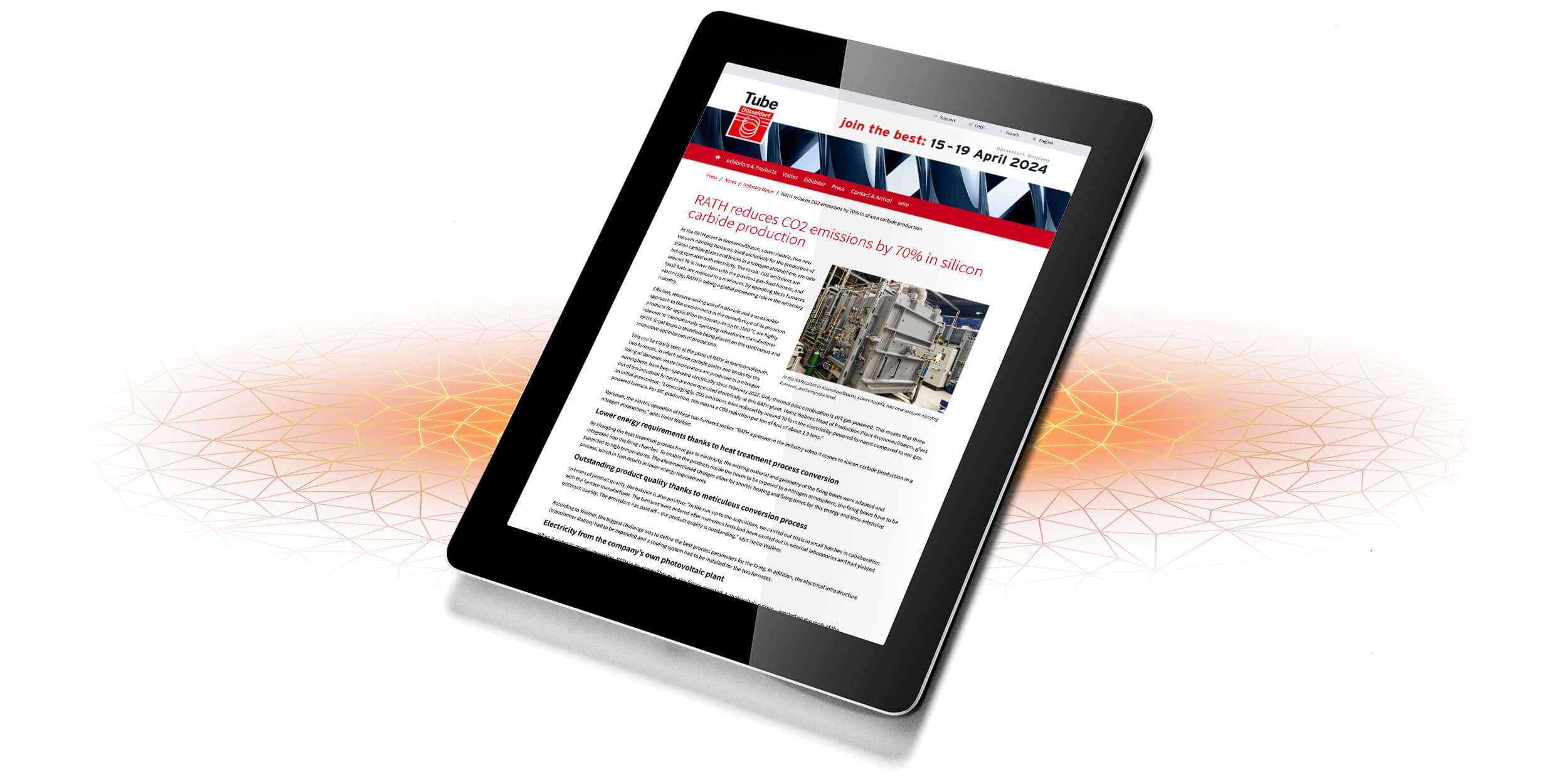
Efficient, resource-saving use of materials and a sustainable approach to the environment in the manufacture of its premium products for application temperatures up to 1800 °C are highly relevant to internationally operating refractories manufacturer RATH. Great focus is therefore being placed on the continuous and innovative optimization of production.
This can be clearly seen at the plant of RATH in Krummnußbaum. Two furnaces, in which silicon carbide plates and bricks for the lining of domestic waste incinerators are produced in a nitrogen atmosphere, have been operated electrically since February 2022. Only thermal post-combustion is still gas-powered. This means that three out of ten industrial furnaces are now operated electrically at this RATH plant. Heinz Wallner, Head of Production Plant Krummnußbaum, gives an initial assessment: “Encouragingly, CO2 emissions have reduced by around 70 % in the electrically-powered furnaces compared to our gas-powered furnace. For SIC production, this means a CO2 reduction per ton of fuel of about 1.9 tons.”
Moreover, the electric operation of these two furnaces makes “RATH a pioneer in the industry when it comes to silicon carbide production in a nitrogen atmosphere,” adds Heinz Wallner.
Lower energy requirements thanks to heat treatment process conversion
By changing the heat treatment process from gas to electricity, the existing material and geometry of the firing boxes were adapted and integrated into the firing chamber. To enable the products inside the boxes to be exposed to a nitrogen atmosphere, the firing boxes have to be subjected to high temperatures. The aforementioned changes allow for shorter heating and firing times for this energy and time-intensive process, which in turn results in lower energy requirements.
Outstanding product quality thanks to meticulous conversion process
In terms of product quality, the balance is also positive: “In the run-up to the acquisition, we carried out trials in small batches in collaboration with the furnace manufacturer. The furnaces were ordered after numerous tests had been carried out in external laboratories and had yielded optimum quality. The procedure has paid off – the product quality is outstanding,” says Heinz Wallner.
According to Wallner, the biggest challenge was to define the best process parameters for the firing. In addition, the electrical infrastructure (transformer station) had to be expanded and a cooling system had to be installed for the two furnaces.
Electricity from the company’s own photovoltaic plant
When it comes to energy generation, RATH in Krummnußbaum is also future-oriented: A photovoltaic system – erected on the roofs of the factory halls – was put into operation in 2020. This 696 kWp photovoltaic plant generates up to 700 MWh per year, which means that around 20 % of the daily electricity requirement currently comes from solar energy. This means a reduction of around 350 tons in CO2 emissions per year. Since 2020, around 99 % of the electricity produced annually by this self-consumption plant has been used directly at the Krummnußbaum plant. Any surplus energy is fed back into the grid.
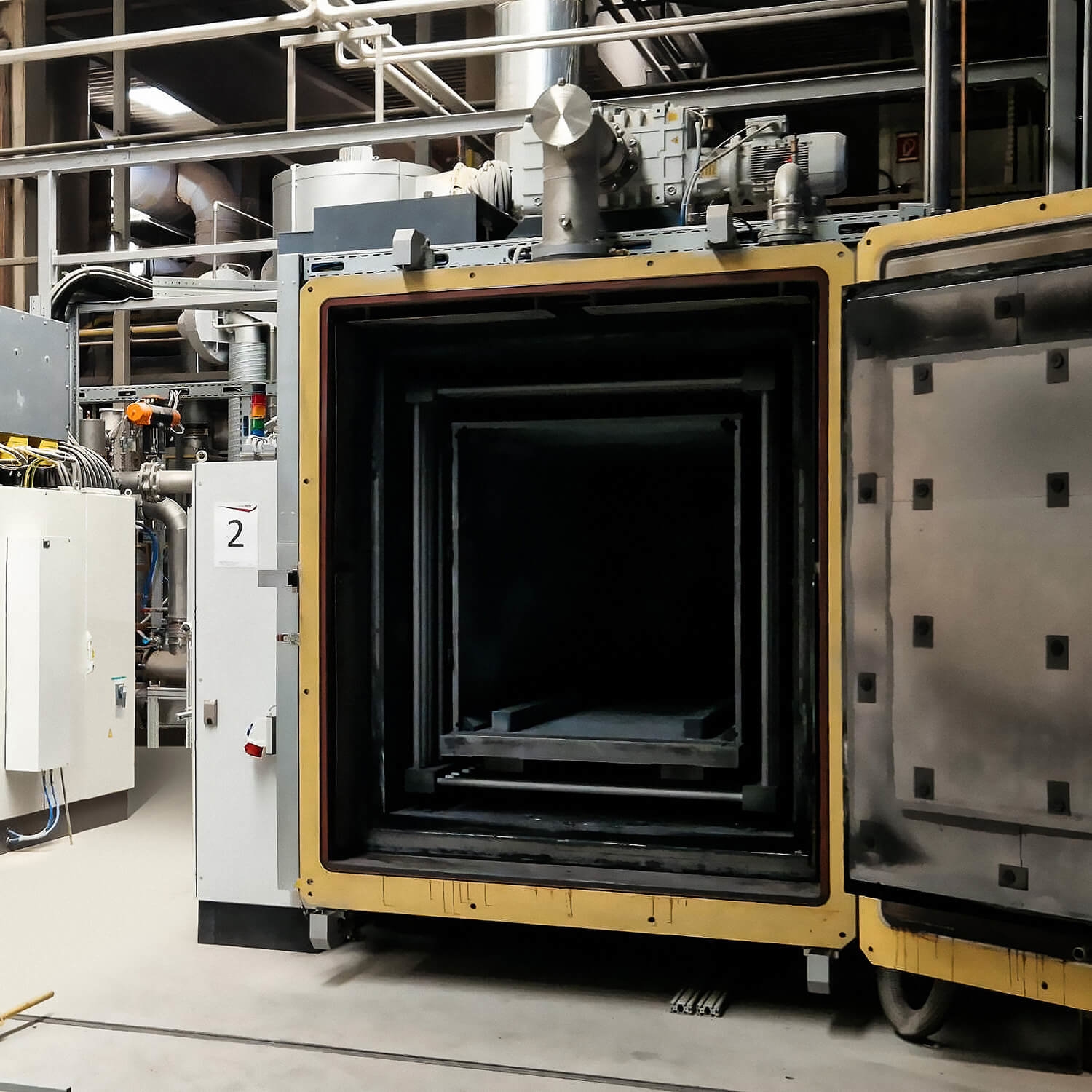