Use of hydrogen in steel production: Refractories manufacturer RATH to present groundbreaking results of a study on the effects on refractories
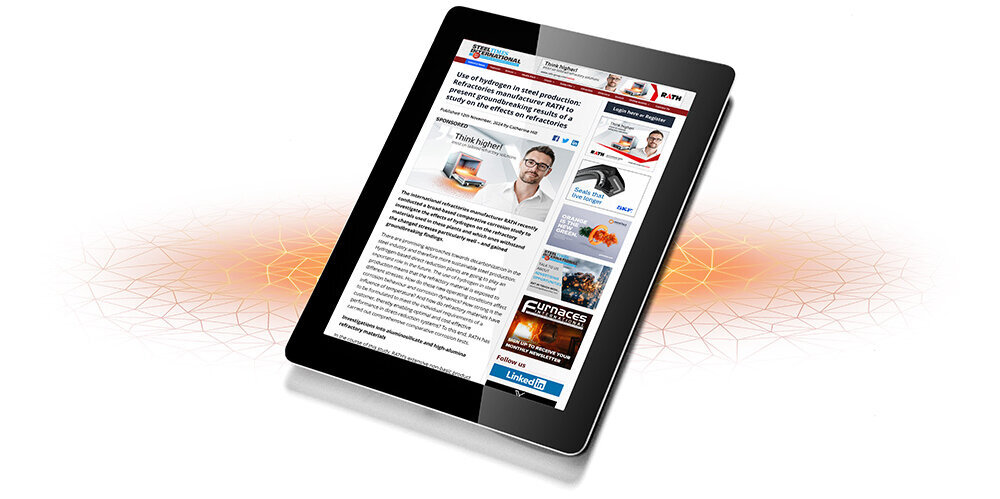
Vienna, October 28, 2024
The use of hydrogen in steel production means that the refractory material is exposed to different stresses. How do these new operating conditions affect corrosion behavior and corrosion dynamics? How strong is the influence of temperature? And how do refractory materials have to be formulated to meet the individual requirements of a customer, thereby enabling optimal and cost-effective performance in direct-reduction systems? To this end, RATH has carried out comprehensive comparative corrosion tests.
Investigations into aluminosilicate and high-alumina refractory materials
In the course of this study, RATH’s extensive non-basic product portfolio with a composition of 40–99 % Al2O3 was exposed to an H2 atmosphere. Samples of lightweight refractory bricks, dense bricks, monolithic products, mats made of high-temperature wool and vacuum-formed parts were evaluated. The corrosion tests were carried out at the German Institute for Refractories and Ceramics (DIFK).
The temperature exposure was 1250 °C and 1400 °C in a 100-% H2 atmosphere, with an exposure time of 200 hours. In addition, aging at 1100 °C under a typical mixed gas atmosphere was performed specifically for use in direct reduction plants. Corrosion was assessed by determining the mass loss in order to be able to make statements about temperature dependency and corrosion rate. In addition to determining the physical properties, further chemical analyses and X-ray diffractometry measurements were carried out before and after exposure to provide further information on phase stability and new mineral formation.
Important findings from the study:
- High-corundum materials show very good corrosion resistance in all products.
- Under certain conditions (selected raw material usage and production parameters), mullite likewise proves
a suitable material in an atmosphere containing hydrogen. - Glass phases and SiO2 phases are significantly reduced in the presence of high hydrogen contents.
- Foreign oxides and impurities in the overall system play a significant role with regard to stability in a hydrogen atmosphere.
- The porosity of refractory materials has only a minor influence on corrosion.
- In the temperature range of 1250 °C - 1400 °C, a significant increase in the corrosion rate was recorded.
- Phosphate-bonded fired bricks are only slightly more resistant to corrosion than phosphate-free products.
In summary, RATH’s study results are highly relevant for future material selection in the respective application. The targeted further development of refractory materials and systems is particularly important for the transition to direct-reduction plants with additional hydrogen admixture and the goal of producing steel in a completely climate-neutral way in the future.
Contact:
Anja Rauter
Global Manager Marketing Communications
T +43 1 513 44 27 - 21 76
E anja.rauter@rath-group.com
Thomas Binder-Krieglstein
Head of Group Marketing
T +43 1 513 44 27 - 21 74
E thomas.binder-krieglstein@rath-group.com