RATH at Glassman USA 2023 – from energy saving refractory solutions to hot gas filtration in the glass industry: Learn from the RATH experts how you can act even more sustainably
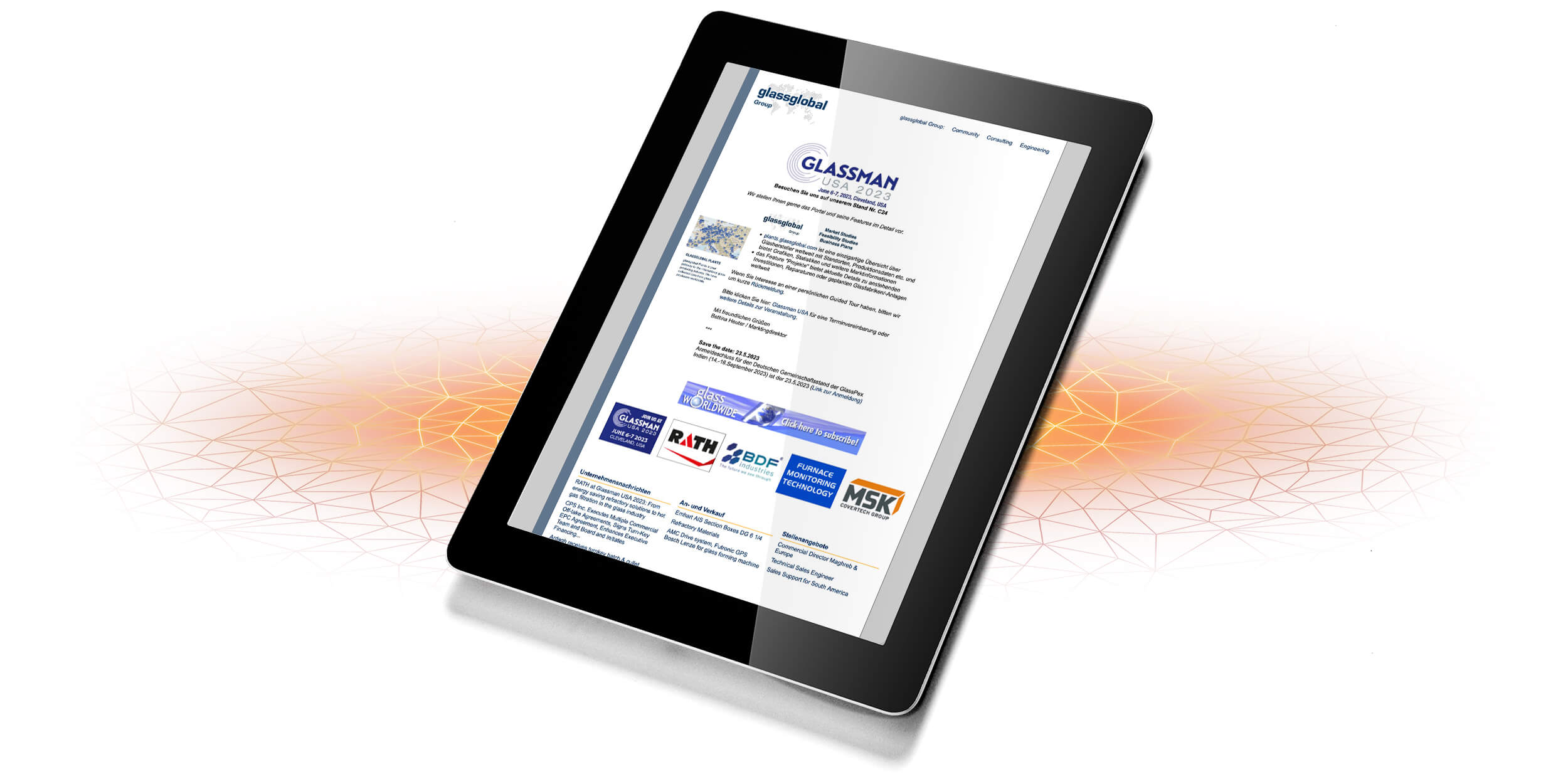
Ambitious efforts are underway, and the Austrian refractory manufacturer RATH is intensively supporting its customers – with innovative products for refractory linings as well as hot gas filter elements to filter particle-laden industrial flue gases. Comprehensive information is available from RATH's experts at the RATH booth at Glassman USA. In addition RATH will also be represented at Glassman USA with an expert lecture on hot gas filtration in the glass industry: Manfred Salinger, Director Advanced Ceramic Filtration Solutions RATH Group, will present a holistic approach to emission control and heat recovery at his lecture.
With more than 130 years of experience, RATH is regarded as a competence leader in the refractory sector and offers the complete range of premium refractory materials for the entire glass manufacturing process. The continuous further development of refractory compositions is a challenge that RATH is taking on with great commitment which is also proven by the new RATH product series. “The new FOURATH 4xx feeder expendable series is based on an optimized formulation which has been exclusively developed and produced by RATH”, says Robert Nusszer, Managing Director of the Sales Unit Glass at RATH. “The product has been put through its paces in our laboratories and has successfully passed the first glass factory trials in the last 2 years.”
From improved crack and thermal shock resistance to longer service life
While the previous 3xx mixes (like 333, 315, 301, 338, 345, etc.) were produced using the slipcasting technique, the new FOURATH 4xx mixes are produced using a so-called hybrid technology: RATH uses the same mold park, but a special vibrocasting technology. “This brings some significant advantages: For example, the new feeder expendable series convinces with improved product quality – due to a more compact mix and better surface quality”, says Robert Nusszer. “We selected the highest quality raw materials in order to keep the impurity level to a minimum, to prevent blister formulation. Furthermore, we now can avoid the additional grinding, e. g. of the tube´s outer surface – thus, we are able to increase the service life of the tube.” The thermal shock resistance has also significantly improved and the risk of cracking has decreased considerably.
At the recent international glass trade fairs, the following products were shown: the already well tested and released 420 (a complementary mix of 333, 315) – tubes, plungers, orifice rings and stirrers as well as the new 473 zirconia inserted spouts. The new fused silica mixes, the drain-cast 457 and the slip-cast 458 were also introduced. These mixes are used in the highest quality glass production, e. g. in melting crucibles, and the 458 is also available, for example, for crown repair of glass melting tanks, as well as suspended brick in the doghouse. “It is a very important step ahead that we have recently resumed the manufacturing of forehearth 333 channel blocks at our US-facility in Owensville, as well as producing the first front channel blocks for trial purposes in mix 420, responding to serious market demand. Furthermore, at our Budapest facility, we have set up a significant production capacity for producing high-alumina channel blocks”, Robert Nusszer adds.
RATH expert lecture on hot gas filtration at Glassman USA
A company with more than 130 years of experience in refractory technology is also predestined for hot gas filtration. So it’s only logical that the internationally renowned refractory manufacturer also specializes in this field. For many years, RATH has been developing innovative ceramic hot gas filter elements, which make it possible to filter particle-laden industrial flue gases at temperatures up to 1000 °C and to reduce emissions of nitrogen oxides.
Manfred Salinger, Director Advanced Ceramic Filtration Solutions RATH Group, will present a holistic approach to emission control and heat recovery at his lecture at Glassman USA. In addition the proven expert on hot gas filtration will compare the improved emission control system with the conventional solution, introduce the range of available filter element lengths and review the lessons learned and the keys to reliable operation and long service life of the filter elements.
“In order to reduce the footprint of the emission control equipment, hot gas filters can now be equipped with ceramic filter elements up to 20 feet long. The new generation of longer filter elements lowers capital investment costs while maintaining the important functions of particulate removal and selective catalytic reduction of nitrogen oxides”, Manfred Salinger says in a preview of his presentation.
Meet our experts at the RATH booth at Glassman USA and learn more about our premium refractory solutions for the glass industry.
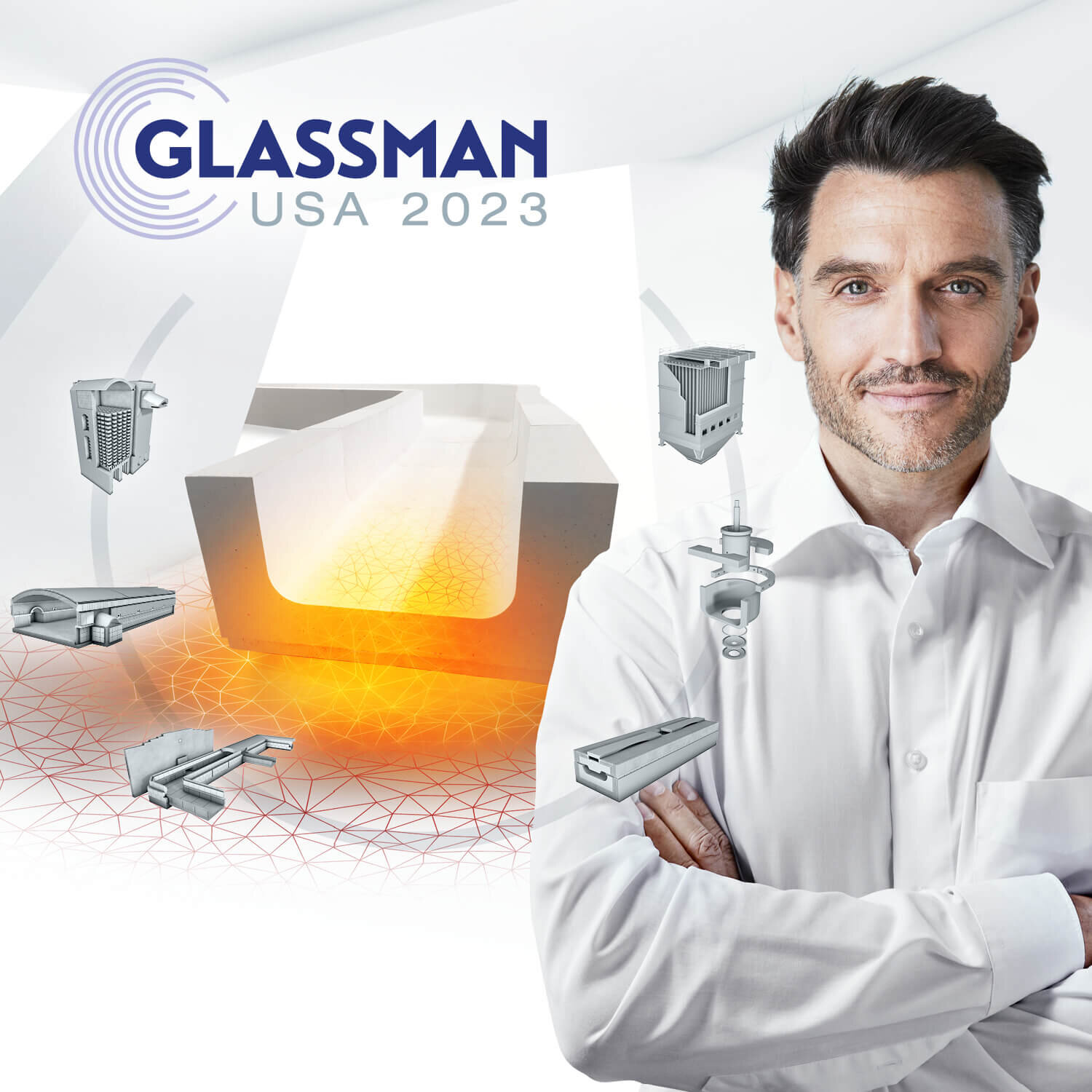