Austrian refractories manufacturer RATH supports its customers with comprehensive engineering know-how and energy-saving refractory solutions
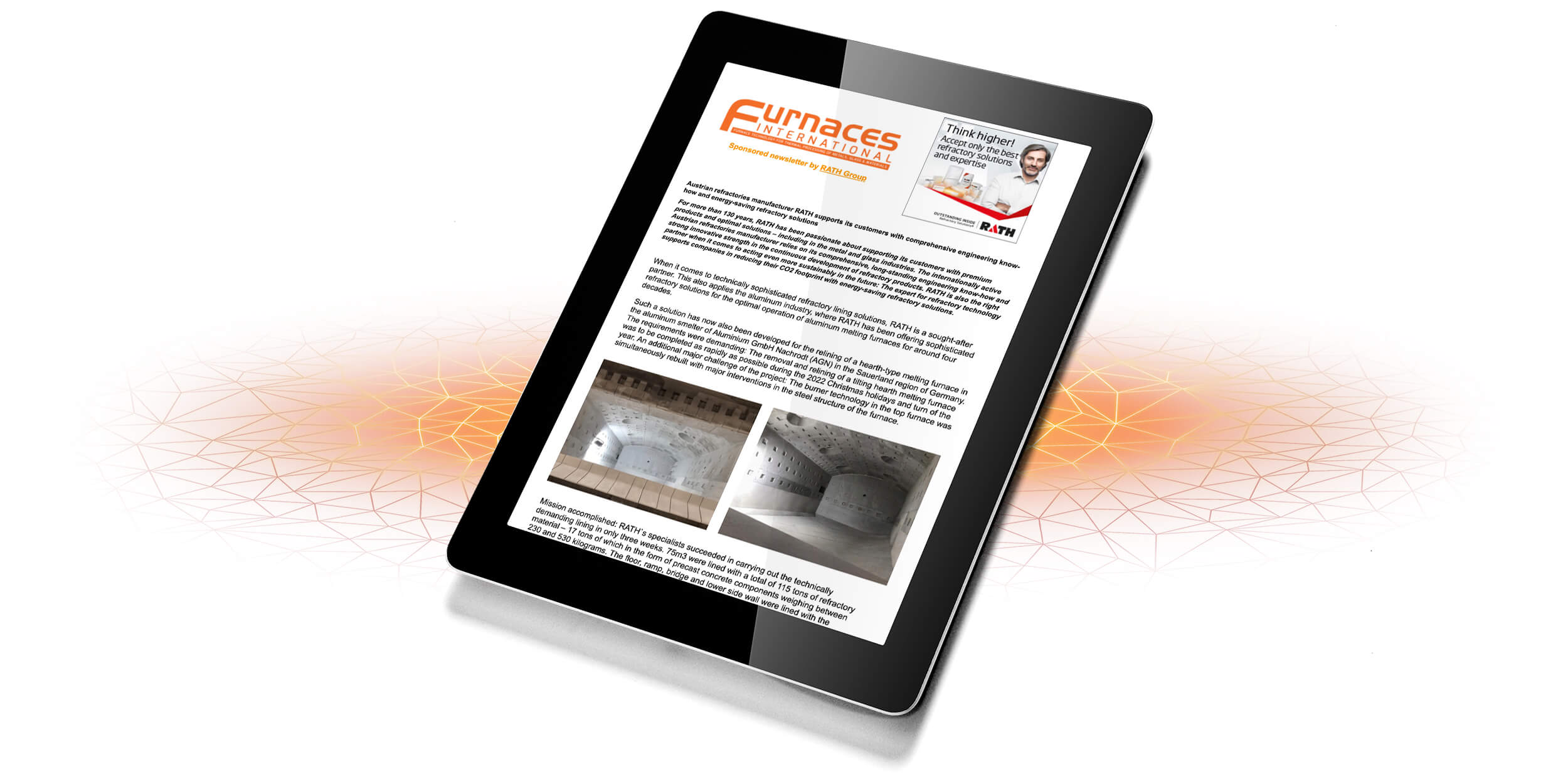
The internationally active Austrian refractories manufacturer relies on its comprehensive, long-standing engineering know-how and strong innovative strength in the continuous development of refractory products. RATH is also the right partner when it comes to acting even more sustainably in the future: The expert for refractory technology supports companies in reducing their CO2 footprint with energy-saving refractory solutions.
When it comes to technically sophisticated refractory lining solutions, RATH is a sought-after partner. This also applies the aluminum industry, where RATH has been offering sophisticated refractory solutions for the optimal operation of aluminum melting furnaces for around four decades.
Such a solution has now also been developed for the relining of a hearth-type melting furnace in the aluminum smelter of Aluminium GmbH Nachrodt (AGN) in the Sauerland region of Germany. The requirements were demanding: The removal and relining of a tilting hearth melting furnace was to be completed as rapidly as possible during the 2022 Christmas holidays and turn of the year. An additional major challenge of the project: The burner technology in the top furnace was simultaneously rebuilt with major interventions in the steel structure of the furnace.
Mission accomplished: RATH`s specialists succeeded in carrying out the technically demanding lining in only three weeks. 75m3 were lined with a total of 115 tons of refractory material – 17 tons of which in the form of precast concrete components weighing between 230 and 530 kilograms. The floor, ramp, bridge and lower side wall were lined with the proven component concept. Furthermore, Nachrodt relied on RATH's experts when it came to heating: The plant was heated externally with built-in steam pressure and temperature sensors in the refractory lining of the bath.
Steel industry: RATH combi-modules make heat treatment furnaces more energy-efficient
Reducing pollutant emissions, optimizing energy use – the steel industry, like other industries, is also facing the major challenge of acting more sustainably and drastically reducing its carbon footprint. These are challenges where RATH, as one of the most renowned specialists for refractory technology – especially for heat treatment in the steel industry – intensively supports its customers. Whether high-temperature wool, lightweight refractory bricks, concretes or dense bricks, the RATH engineering experts always find the best technical and economical solution for the requirements of the heat treatment industry. For example, a bogie hearth forging furnace is lined with a mix of different RATH products: Combi-modules in the upper furnace and roof, but dense castable solutions for the lower walls and the kiln car, which guarantees optimum, energy-efficient lining. Combi-modules are one of many proven products RATH relies on, e. g. for the refractory lining of forging furnaces: a combination of different high-temperature wool qualities provides a technically and economically optimal solution. These modules are available according to specific customer requirements and are produced in a wide variety of shapes and sizes.
RATH offers a comprehensive range of premium refractory solutions and products for the entire spectrum of continuously or discontinuously operated steel heat treatment furnaces. In addition, the refractory expert is ready for the future: RATH refractory materials can also be used to line electrically heated and also hydrogen-fired furnaces.
FOURATH: New feeder expendable series brings significant advantages in glass production
Ambitious efforts to reduce the carbon footprint are also underway in the glass industry, and RATH is intensively supporting its customers with innovative products for refractory linings. The further development of refractory compositions is a challenge that RATH is taking on with great commitment which is also proven by a new RATH product series: The new FOURATH 4xx feeder expendable series is based on an optimized formulation which has been exclusively developed and produced by RATH. It has been put through its paces in the RATH laboratories and has successfully passed the first glass factory trials over the last 2 years.
From better crack and thermal shock resistance to longer service life
While the previous 3xx mixes – like the well-known 333, 315, 301, 338, 345, etc. – were produced using the slipcasting technique, the FOURATH 4xx mixes are manufactured using a so-called hybrid technology. RATH uses the same mold park, but casting is no longer done by slipcasting; instead, a special vibro-casting technology is used. This brings some significant advantages: For example, the new feeder expendable series convinces with improved product quality – due to a more compact mix and better surface quality.
RATH selected the highest quality raw materials in order to keep the impurity level to a minimum, to prevent blister formulation. Furthermore, the additional grinding, e. g. of the tube´s outer surface, can now be avoided – thus, RATH is able to increase the service life of the tube.
Other positive consequences of the new manufacturing technology: The thermal shock resistance has also significantly improved and the risk of cracking has decreased considerably.
Speaking of which, the new product series is among the topics you can learn more about at the RATH booth at Glassman USA (June 6-7, Cleveland).
www.rath-group.com/metals
www.rath-group.com/glass
www.rath-group.com/aluminum
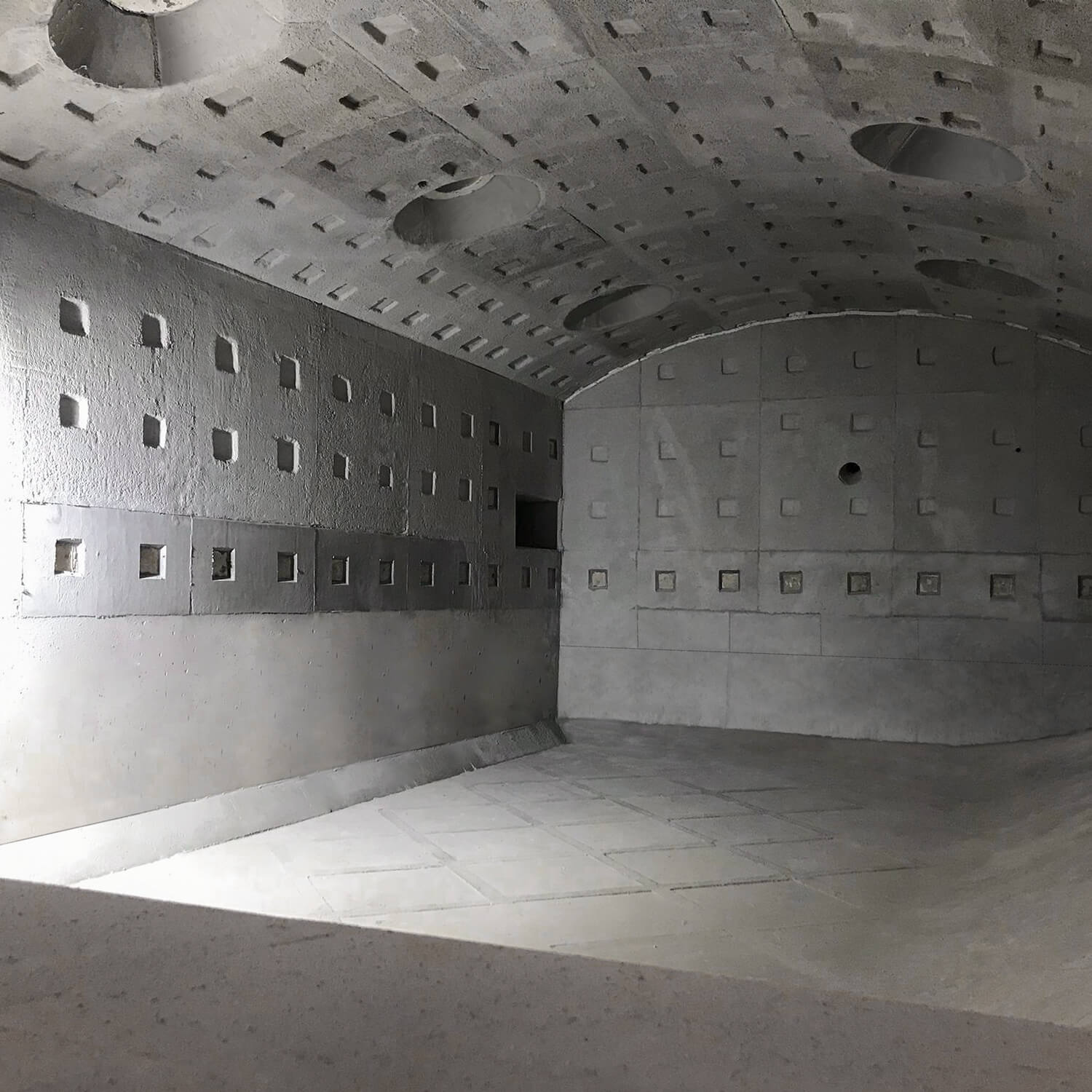