Supporting the glass industry in its sustainability efforts remains at the top of RATH's agenda in 2024
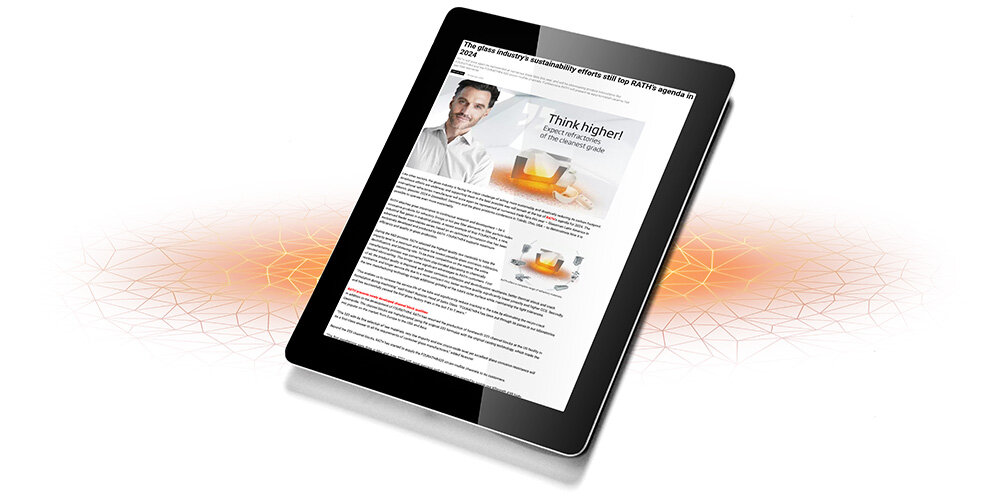
Vienna, February 27, 2024
Thus, RATH attaches great importance to continuous research and development – be it innovative products for refractory linings or hot gas filter elements to filter particle-laden industrial flue gases in industrial plants. A recent example of this: FOURATH®4, a new, advanced feeder expendables series, based on an optimized formulation that has been exclusively developed and produced by RATH. FOURATH®4 supports maximum efficiency and quality in glass production.
During the R&D process, RATH selected the highest quality raw materials to keep the impurity level to a minimum and achieve the lowest possible glass corrosion, infiltration, devitrification, and blistering rate. To be more competitive on the market, the entire manufacturing process was converted from clay-bonded slipcasting to chemically bonded vibrocasting. This brings some significant advantages to RATH customers. First of all, the product quality is improved, with better corrosion, infiltration and devitrification resistance, better thermal shock and crack resistance, and longer service life due to a more compact mix, better surface quality, significantly lower porosity and higher CCS. Secondly, the new manufacturing technology avoids additional grinding of the tube’s outer surface while maintaining the tight tolerances. “This enables us to increase the service life of the tube and significantly reduce cracking in the tube by eliminating the micro-crack formulation during machining,” Robert Nusszer, Head of Sales Glass, says. “FOURATH®4 has been put through its paces in our laboratories and has successfully passed the first glass factory trials in the last 2-3 years.”
RATH presents newly developed channel block qualities
In addition to the development of FOURATH®4, RATH has resumed the production of forehearth 333 channel blocks at the US facility in Owensville. The channel blocks are manufactured using the original 333 formulas with the original casting technology, which made the mix popular on the market, from Europe to the USA and Asia. “The 333 with its fine selection of raw materials, very low impurity and low zircon-oxide level yet excellent glass corrosion resistance will be a first-class answer to all the requirements of container glass manufacturers,” adds Nusszer.
Beyond the 333 channel blocks, RATH has started to supply the FOURATH®420 zircon-mullite channels to its customers. “The first installations were done in May/June 2023 with great success and we have also started to supply our Vibrorath K99 high-alumina channel blocks to the glass industry. The initial installations of high-alumina channels were successfully put into operation over the last couple of years. Currently we have several ongoing projects in the production phase, and in 2024 we will continue to expand our forehearth business segment, offering a complete refractory package to our customers”, Nusszer summarizes.
Ready for the future with ceramic hot gas filter elements
RATH also helps the glass industry to meet the highest emission protection requirements in industrial plants: Hot gas filtration is becoming increasingly important here.
For many years, the company has been developing innovative ceramic hot gas filter elements that make it possible to filter particle-laden industrial flue gases at temperatures up to 1000 °C and reduce emissions of nitrogen and sulfur oxides, as well as reduce the emission of fine particulates.
The RATH facility in Meißen (Germany) is home to cutting-edge facilities for the manufacture of RATH´S FILTRATH® non-catalytic and FILTRATH®CAT catalytic filter elements. RATH ceramic hot gas filters are produced in Europe using RATH fibers and available in lengths from 1 to 6 meters.
"Early removal of dust from particulate-contaminated exhaust gases at high temperatures is a requirement that makes sense, not only from an ecological but also from an economic point of view. The use of RATH ceramic filter cartridges leads to a better energy balance as there is no need to down- and up-regulate the exhaust gas temperature. Uneconomical cooling of exhaust gases solely for filtering is no longer necessary, which also saves costs", summarizes Robert Nusszer and adds: "Purified hot gas can also be used for other applications, for example to generate energy or hot water. This is another decisive advantage."
www.rath-group.com/hot-gas-filtration
Contact:
Anja Rauter
Global Manager Marketing Communications
T +43 1 513 44 27 - 21 76
E anja.rauter@rath-group.com
Thomas Binder-Krieglstein
Head of Group Marketing
T +43 1 513 44 27 - 21 74
E thomas.binder-krieglstein@rath-group.com
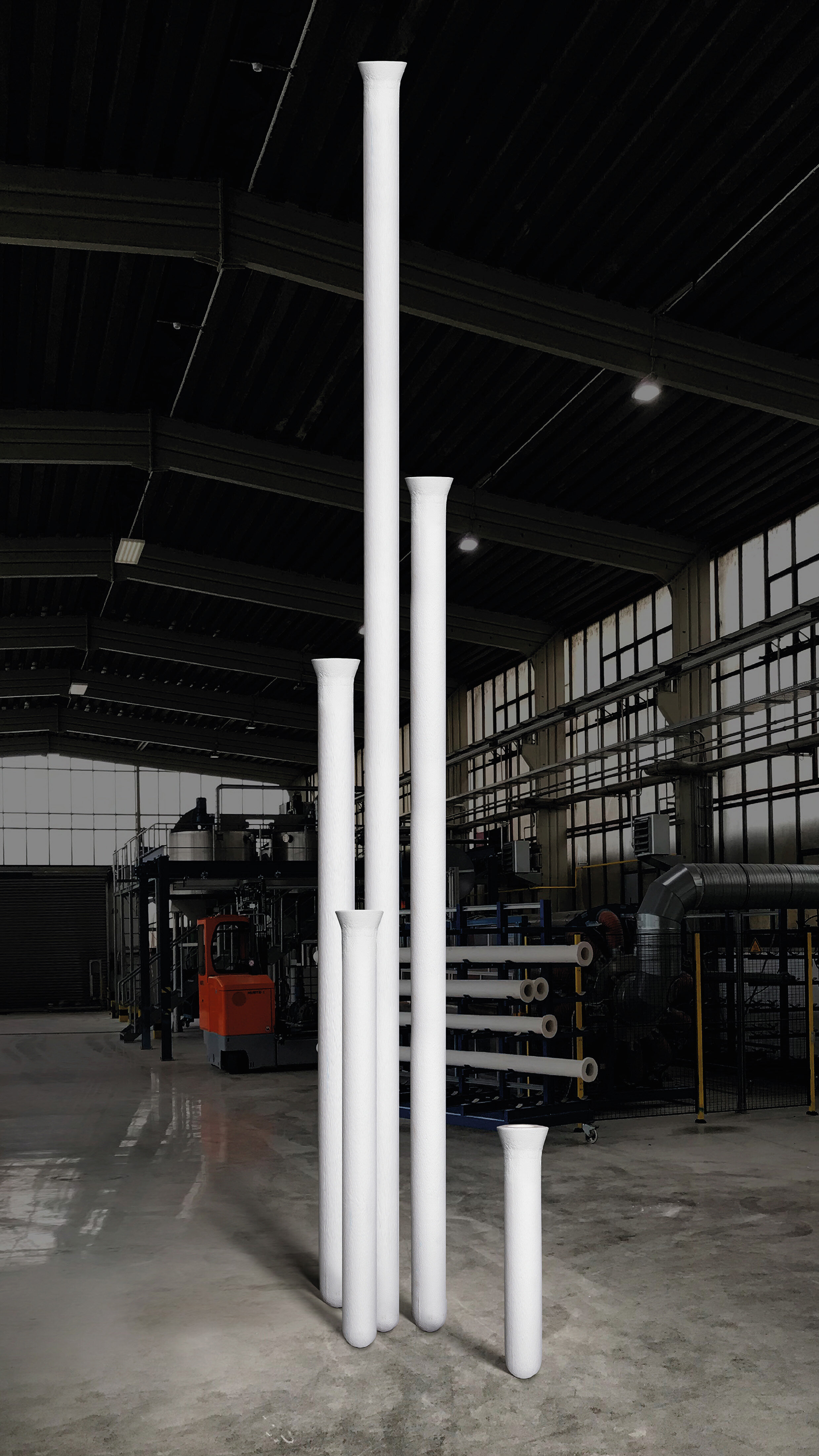