RATH presents its latest product developments at Glassman Asia 2023 – from energy saving refractory solutions to hot gas filtration
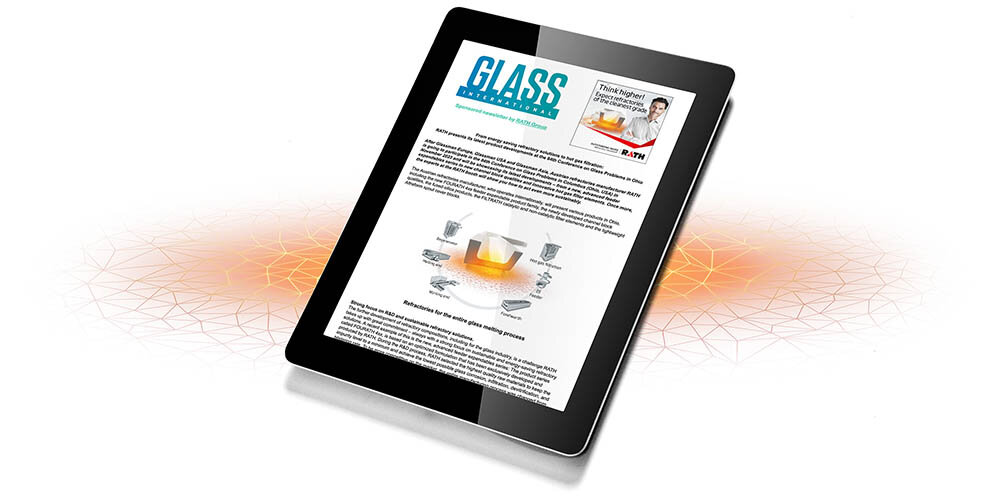
“The Asian market is very important to RATH, especially for the feeder expendable business. As for our high-quality, high added-value products, we are seeing significant growth potential in the region. Therefore, we are especially pleased to participate in the Glassman Asia exhibition in South Korea this year and to present our latest product developments,” says Robert Nusszer, Head of Sales Glass, RATH.
The Austrian refractories manufacturer, who operates internationally, will present various products in Seoul, including the new FOURATH 4xx feeder expendable product family, the newly developed channel block qualities, the fused-silica products, the FILTRATH catalytic and non-catalytic filter elements and the lightweight Altraform spout cover blocks.
Strong focus on R&D and sustainable refractory solutions.
The further development of refractory compositions, including for the glass industry, is a challenge RATH takes up with great commitment – always with a strong focus on sustainable and energy-saving refractory solutions. A recent example of this is the new, advanced feeder expendables series: The product series called FOURATH 4xx, is based on an optimized formulation that has been exclusively developed and produced by RATH. During the R&D process, RATH selected the highest quality raw materials to keep the impurity level to a minimum and achieve the lowest possible glass corrosion, infiltration, devitrification, and blistering rate. To be more competitive on the market, the entire manufacturing process was changed from slipcasting to vibrocasting by using the same mold park.
This brings some significant advantages to RATH customers. First of all, the product quality is improved, with better corrosion, infiltration and devitrification resistance, better thermal shock and crack resistance, and longer service life due to a more compact mix, better surface quality, significantly lower porosity and higher CCS. Secondly, the new manufacturing technology avoids additional grinding of the tube’s outer surface while maintaining the tight tolerances. “This enables us to increase the service life of the tube and significantly reduce cracking in the tube by eliminating the micro-crack formulation during machining,” Robert Nusszer summarizes. “The new product series has been put through its paces in our laboratories and has successfully passed the first glass factory trials in the last 2-3 years, which was a very long process, but we are very satisfied with the results.”
RATH also presents the newly developed channel block qualities
“In addition to the development and introduction of the FOURATH 4xx feeder expendable product family, we have recently resumed the production of forehearth 333 channel blocks at our US facility in Owensville,” says Robert Nusszer. The channel blocks are manufactured using the original 333 formulas with the original casting technology, which made the mix popular on the market, from Europe to the USA and Asia. “The 333 with its fine selection of raw materials, very low impurity and low zircon-oxide level yet excellent glass corrosion resistance will be a first-class answer to all the requirements of container glass manufacturers,” adds Nusszer.
RATH expert lecture on hot gas filtration at Glassman Asia
A company with more than 130 years of experience in refractory technology is also predestined for hot gas filtration. So it’s only logical that the internationally renowned refractory manufacturer also specializes in this field. For many years, RATH has been developing innovative ceramic hot gas filter elements, which make it possible to filter particle-laden industrial flue gases at temperatures up to
1000 °C and to reduce emissions of nitrogen oxides.
Manfred Salinger, Head of Advanced Ceramic Filtration Solutions RATH Group, will present a holistic approach to emission control and heat recovery at his lecture at Glassman Asia. In addition the proven expert on hot gas filtration will compare the improved emission control system with the conventional solution, introduce the range of available filter element lengths and review the lessons learned and the keys to reliable operation and long service life of the filter elements.
“In order to reduce the footprint of the emission control equipment, hot gas filters can now be equipped with ceramic filter elements up to 20 feet long. The new generation of longer filter elements lowers capital investment costs while maintaining the important functions of particulate removal and selective catalytic reduction of nitrogen oxides”, Manfred Salinger says in a preview of his presentation.
Meet our experts at Glassman Asia (September 20-21, Seoul) at the RATH booth and learn more about our premium refractory solutions for the glass industry.
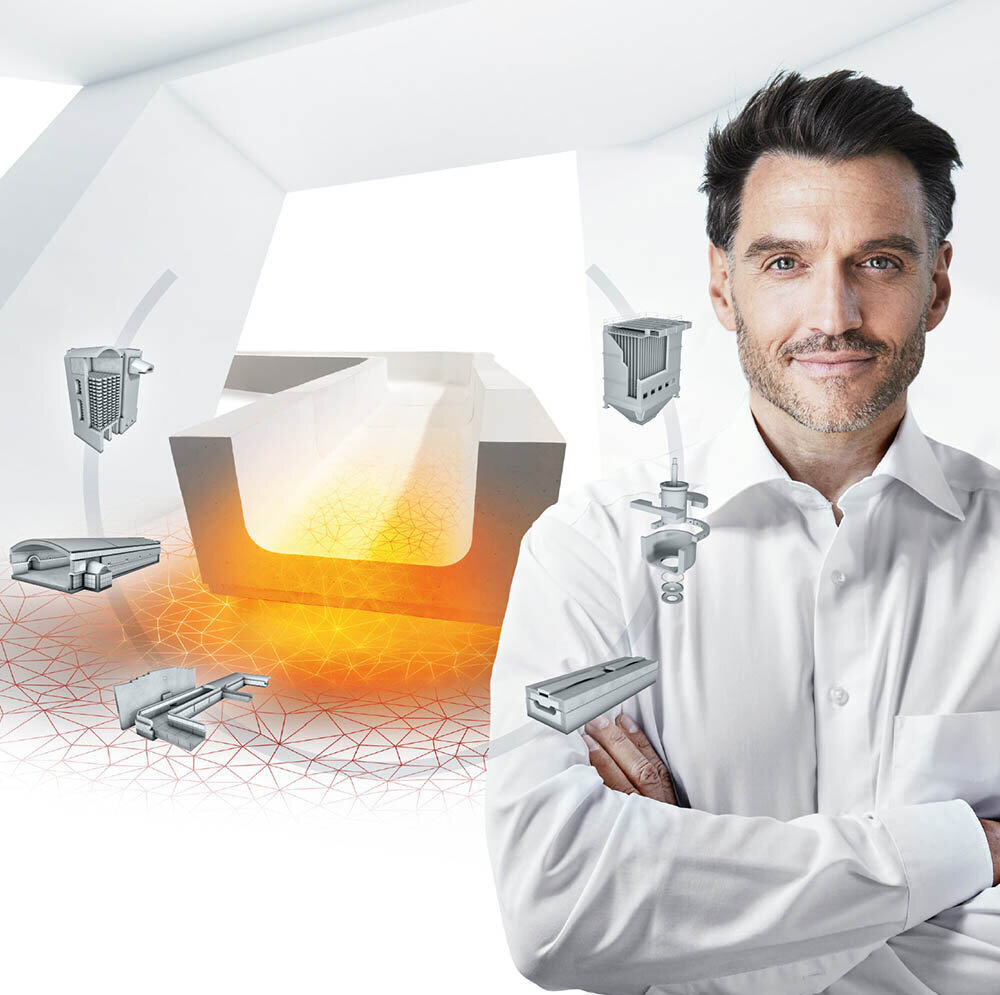